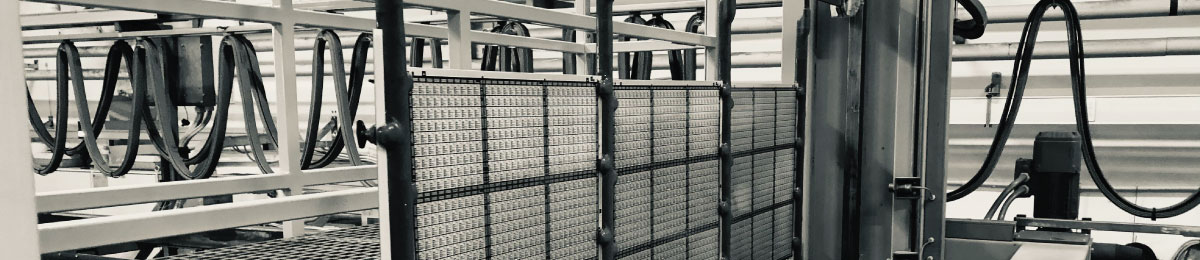
Silga is a leader company in galvanic treatments, and surface finishings. Its PCBs division can get all the know-how from that, never reached from anyone else in the same sector.
Thank’s to the big variety of surface finishings, Silga become a primacy for:
- Range of products
- Innovation
- Realiability
Passivated Copper
This process consists in protecting copper with a layer formed by particular organic substances, with indicative thickness of 0,3 µm. The result is a surface absolutely uniform and planar.
Today’s copper passivation processes are designed to withstand multiple soldering cycles, also lead-free type; the solder joint is formed directly between tin and copper.
The passivated copper finishing, compliant to RoHS Directive, is the least aggressive towards the printed circuit board in terms of chemical and thermal and, if necessary, it can be reworkable.
Immersion Silver
The Immersion Silver process consists in the deposition of an extremely even and planar silver layer.
The thickness ranges from 0.15 to 0.5 µm and provides excellent solderability with both traditional and lead-free alloys; the solder joint is formed directly between tin and copper.
The chemistry of the process works at low temperature and is designed to give to the silver layer a high resistance to oxidation.
This Immersion Silver finishing is in compliance with the RoHS Directive
Mixed finishing
If necessary, it is possible to apply different surface finishings on the same PCB. This occurs in the case when, for example, on a printed circuit there are simultaneously required contacting areas to be realized in Electrolytic Gold-Nickel and other areas, dedicated to SMT assembly, where passivated copper or ENIG finishing are needed.
Hot Air Solder Levelling
During this process, which today still represents the most common method of solderable surface finishing, the printed circuit board, after the soldermask step, is immersed in a molten Tin-Lead alloy and, during the subsequent extraction step it is hit by jets of hot air at high pressure which have the task of “leveling” the deposit, removing the excess of alloy from the holes and the pads.
Despite the considerable experience aquired, given that it is a historical finish, the flatness of the HASL finishing is strictly dependent on the circuit lay-out, with thicknesses that can be very variable.
On the other hand it is an easily inspectable finishing and maintains good characteristics of solderability over time, even with multiple soldering cycles; the solder joint is formed between tin and copper.
Hot Air Solder Levelling (lead free)
The operating mechanism of this process is the same of the traditional Hot Air Solder Levelling, with the difference that the alloy used is free from lead, in such a way as to make the surface finish compliant with the RoHS Directive.
The alloys used are usually tin based, with small amounts of silver and copper, but alloys containing nickel also exist.
In consideration that the eutectic point of these alloys is higher than those based on Sn/Pb, the working temperature of HASL Lead-Free is higher and therefore the greater thermal stress to the printed circuit board should be taken into consideration.
Electroless Gold Nickel
This surface finish is composed of two layers deposited by chemical processes: a layer of nickel, with a thickness of 3-8 µm, and a subsequent layer of pure gold with a thickness whose value can fluctuate between 0.04 and 0.12 µm. The Gold is the real protective finishing while the nickel is used to prevent the migration of copper into Gold.
It is a planar finish, able to withstand multiple soldering cycles. It is easy to solder, even after long periods of storage; the solder joint is formed between tin and nickel.
The ENIG finishing, which is compliant with the RoHS Directive, is particularly suitable for “fine pitch” printed circuit boards and can be also used for contacting areas.
Electrolytic Gold Nickel
Even if it cannot be considered a solderable surface finishing, this process is applied, generally after the solder mask, to protect the contacting elements, especially when a high number of operations is required during the service life (sliding contacts are an example).
In this case, the deposits are obtained through an electrolytic process: at first, a layer of nickel with a thickness of at least 5 µm is deposited, followed by a layer of gold with variable thickness, depending on customer’s specification, even up to 3 µm.
The deposit of gold contains a small percentage of a metal binder (generally Cobalt) that gives the necessary characteristics of hardness (“Hard Gold“).
Immersion Tin
The immersion tin process consists in the chemical deposition a layer of tin with a thickness variable between 0.8 and 1.2 µm. It is a finishing in accordance with the RoHS Directive which offers excellent characteristics of flatness and which is able to withstand multiple soldering cycles, also lead-free.
The solder joint is formed directly between tin and copper. The printed circuit boards with chemical tin finishing are suitable for press-fit mounting technology also.
Electrolytic Tin
The Electrolytic Tin process is one of the possibilities that Silga, given the considerable experience in the galvanic field, is able to offer to fulfill particular requests or special products. In this case, a layer of tin is deposited by an electrolytic process with a thickness from 3 to 10 µm.
This finishing, compliant with the RoHS Directive, can be applied both on rigid and flexible printed circuit boards and ensures in the short term a good solderability.